When developing new or redesigning old products, you have to take into account how the how the product is going to be produced, and that requires an entirely different mindset.
Designing your product to be manufactured consistently with quality is a challenge. Having components that are difficult to build or are time-consuming to assemble adds unnecessary cost.
To minimize costs and warranty issues and to ensure quality remains high, all products need to follow Design for Manufacture and Assembly (DFMA) principles. The DFMA process leads to the lowest cost of manufacturing. There is nearly 3X a difference in the cost as compared to poor designs and inefficient manufacturing processes. Over time, as technology advances, what determines a good DFMA design from a poor one changes—resulting in DFMA a valuable part of the continuous improvement process.
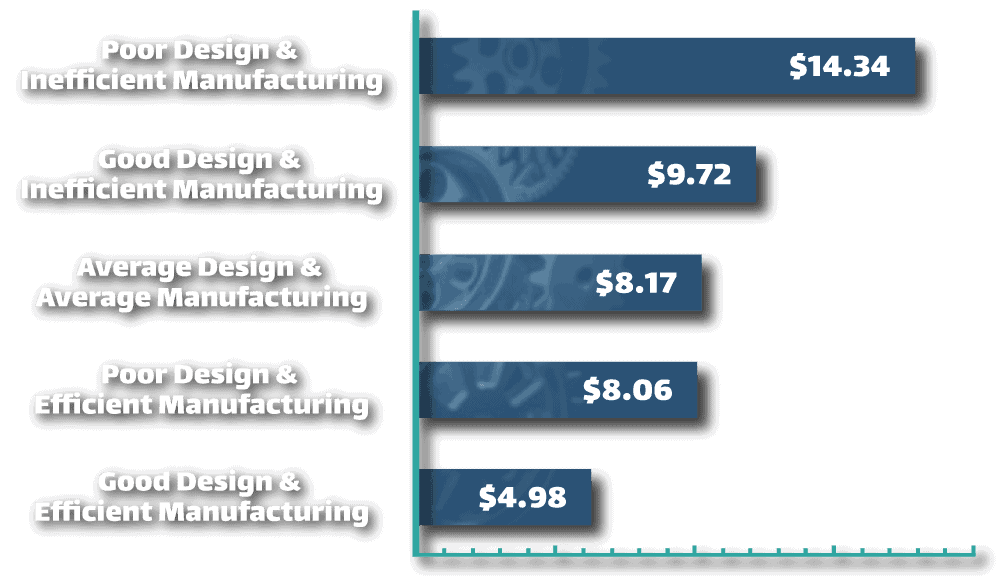