What if you found a way to design a new product or redesign an existing product or part that would generate millions of dollars or even save your company millions in lifetime costs? How would that feel?
Let’s envision a scenario where truth and intelligence dominate; you know a better way to manufacture and assemble your products. But you don’t have the time, capacity, or money to build and test prototype after prototype until you find the faster, better, or cheaper design.
Simulation driven design harnesses the power of Big Data, Computer Aided Design (CAD), and Computer Aided Engineering (CAE) to create a digital prototype of your product or process. Let your team test and prove with scientific certainty that the new design works with the least amount of parts and the best materials to get your products to market.
Empowering you to deliver the lowest total cost design that is sustainable and easily recyclable at the end of its lifecycle. When you simulate your product performance based on data and some engineers’ creativity, you get innovative ideas, leading to you creating game-changing products. And you can run every game-changing product concept through an array of simulations to determine the design that delivers the best traded off of performances, reliability, durability, and total cost.
Companies both large and small rely on the expertise of a trusted engineering advisor to simulate what the perfect product looks like before they ever spend a dollar in prototyping. Simulation saves you resources, money, and, most importantly, the time when developing a new product.
You can run various design scenarios to find the one that meets your metrics or key performance indicators. When you determine the best product or part design before you ever cut anything, you’re already ahead of the game.
How Does Simulation Work?
A computer generated simulation relies on data to create an electronic version of your new or re-engineered product. Simulation allows you to put your product design through several computer generated scenarios to see how your design will function. Identifying areas that need attention before creating a prototype.
Manufacturers and others who rely on innovative design understand the value of simulation driven modeling. You can examine your design and see how your product either achieved your objectives (e.g., fewer parts, enhanced reliability, performance) or needed to be tweaked to produce the perfect design.
These are traditional concerns and represent the costly part of traditional design methodology. Many companies rely on their design engineers to help them achieve better, more cost effective products. Unfortunately, most design engineers don’t have the simulation capability or experience to do a virtual test of a design. Without the data from any type of simulation, finding what needs to be fixed before you build a prototype impossible.
The traditional product design method includes several design models based on feedback from product engineers and others who have a stake in the design. This method examines designs at the end of the design stage before physical testing. Leaving you stuck with fewer options or the ability to make design changes. Escalating costs to redesign when a design doesn’t perform as expected during testing or after being produced.
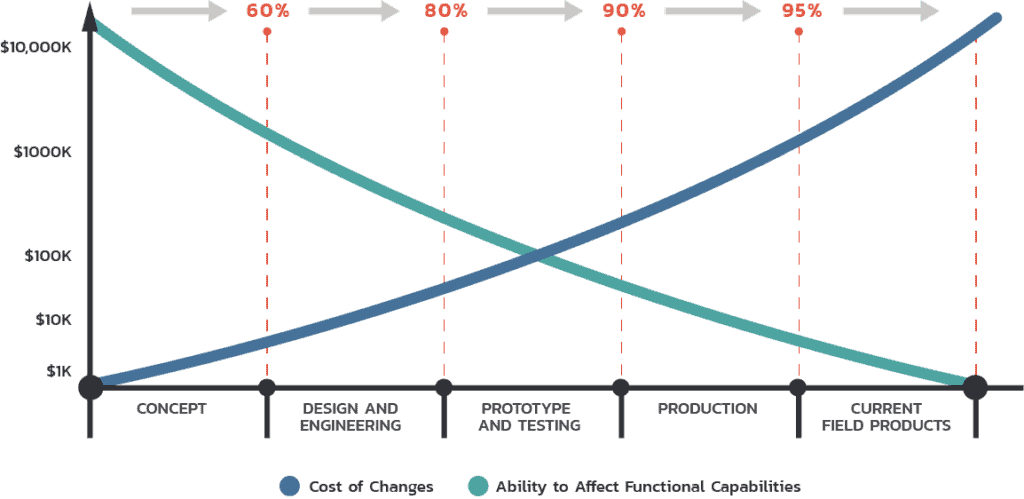
Conversely, simulation driven design moves the design testing too early stages when you start engineering part of the project, removing the risk and cost of redesigning the product design changes that might arise later in the process.
When combined with Designing For Manufacturability and Assembly (DFMA), simulation gets you to a viable finished product faster, cheaper, and with a more targeted components and assemblies than traditional product design offers. Making the simulation driven design a data driven process.
Let’s look at how simulation driven design helps you achieve these benefits. How does a company traditionally design and deliver products?. Product design uses some, all, or more of the following steps in the process to create a product to test:
- Discovery & Product Idea Generation (A Idea is generated whether internally or from a customer)
- Scoping (Technical and Business analysis, Legislation, Competitors, Market Strategy, etc.)
- Business Development (Concept testing, Detailed technical and manufacturing appraisal)
- Engineered and Desing.
- Prototype designed, tested, and if testing is passed, The prototype is certified for production)
- Production
- Aftermarket & Services
A simple and complex process. The traditional method gets expensive and inefficient when the design fails during prototype testing. Redesigning products that don’t make it past testing and certification gets expensive when you have to go back to the drawing board to redesign based on what you learned during testing. Stop and think about it for a moment: what does it cost in time and money to go back to the drawing board to redesign anything?
Performing simulation lets you see where your product/process design won’t behave as intended. Instead of progressing through the traditional design methodology and discovering these problems later in the process(after it has been built), simulation identifies needed changes before you go so far as to create a prototype.
What Simulation Driven Design Offers Companies Instead
Simulation shows you how your design behaves under normal circumstances. Companies need a more efficient process for products, processes, and more to stay competitive. Simulation lets you design for manufacturability and assembly with faster validation of your proposed design.
Your computer aided engineering efforts rely on manufacturing simulations like Computer Fluid Dynamics (CFD) and Finite Element Analysis (FEA), to name a few. These physics-based simulation driven design elements move simulation into the forefront of engineering design, ensuring that the ultimate design is the best design option available. Prototyping becomes the final validation task of a superior design.
Case Study: Simulation Driven Design Shows You Concepts You Won’t See In Labs.
Let’s look at an advanced simulation for your research, development, and validation efforts. Regardless of your aerospace, automotive, biomedical, energy electronics, machinery, or more, simulation capability on your engineering team helps you with the skills you don’t have but need.
Companies like yours use computer aided design (CAD) and engineering (CAE). Instead of using simple CAD or CAE during your process, full simulation captures and reduces the costs at each process stage. More importantly, using FEA and CFD expertise as part of a simulation driven design process allows you to investigate more complex designs and look at fluid processes and solid mechanics design.
Producing prototypes to perform regular or enhanced operational tests that point out weakness in the design often results in project scope and budget overruns. Instead, a CAE simulation at the beginning of the design process delivers data about how your current design performs. Empowering you with the data to propose, validate, and optimize changes that avoid budget overruns or considerable redesign late in the development process.
A simulation driven design allows you to avoid delays that halt your forward progress, which moves your engineering project into a faster, more efficient development process. Simulation engineers with CFD and FEA expertise help you avoid and prevent budget overruns and reduce time to market. When you consider the minimal stages of product design companies commonly progress through, following this methodology leaves you stuck with time consuming, inefficient designs that lead to significant delays.
Computer simulation accelerates the design process, offering answers to questions early in the game. If you continue to design traditional products with physical prototypes or if you don’t change the method at all, you’re leaving yourself open to manufacturing inefficiencies and significantly reducing or eliminating your cost advantage.
Final Thoughts
When you capture a variety of engineering powerhouses designing for manufacturing and assembly (DFMA), simulation driven design, and sustainable design—you get to know much more about your product. Simulations help you discover how various elements affect your products and delivery.
For example, how do you account for supply chains and manufacturing capabilities? You can better project production capabilities, minimize waste, and manage supply chains by relying on the trifecta of engineering specialties (DFMA, simulation, and sustainable design).
A trusted engineering advisor helps you determine an update/redesign of your company’s product that meets or exceeds your current capacity and future production to meet customers’ needs.
For example, a team member can analyze each product, seek alternative forms, and offer a proposed product that achieves your company’s objectives. All without cutting the first prototype.
Simulation driven design helps you reduce costs at each stage compared to the traditional way of doing things. Whether you analyze jet engines or other construction projects, the simulation driven design provides the intelligence you need to investigate complex designs and processes using CFD or FEA.
After experiencing the suggestions in this article, you’ll likely realize there is no going back to pre simulation driven design development. When you adopt this methodology, you automatically stay ahead of the competition, leaving those that fail behind. And while you know your product development gains are amazing, those gains far outweigh the inconvenience of understanding Design For Manufacturability and Assembly (DFMA), Simulation Driven Design, and Sustainability Design.
This combination of designing, engineering, and creating processes allows you to deliver your products at a lower cost while maintaining the highest level of quality. It allows you to produce goods and services that meet or exceed your customers’ demands. This three-legged stool of engineering dominance helps you surpass your competition while creating products and engineering designs that:
- Minimize manufacturing and assembly deficiencies
- Uncover drawbacks when engineering for sustainability
- Use computer generated simulations to make the most of your products and boost customer satisfaction
The determination of who stays ahead of others and who falls behind is clinched during the development process. Upgrading your product development process is ultra demanding, but the gains far outweigh the inconvenience.
The secret to success for any company is having enough data on hand to analyze its products and detailed knowledge of the company and its offerings. It’s all about having the right software and analytical expertise and knowledge base to make educated data-driven decisions.
That’s when you call a trusted engineering advisor.